Global Adoption of Slipcoat® Expected to Transform Mining Operations Worldwide
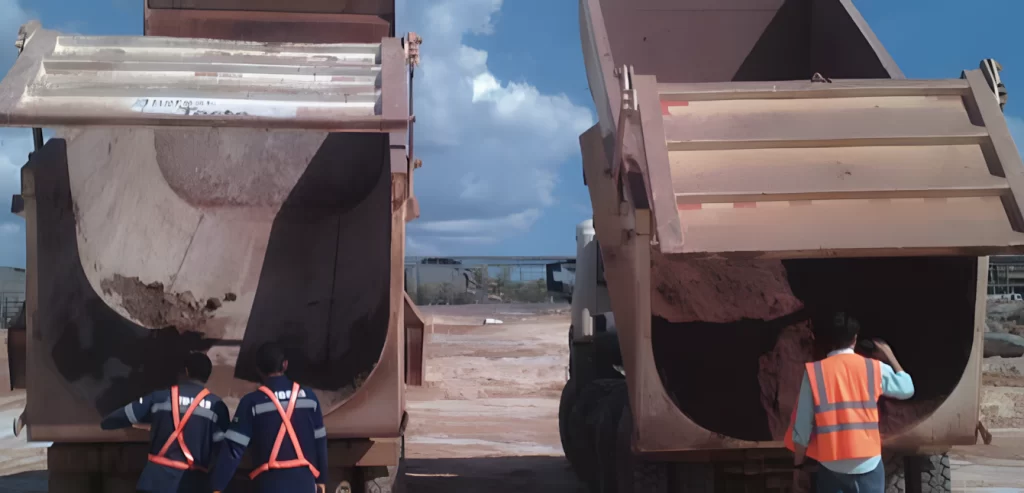
Slipcoat® is revolutionizing mining operations worldwide by addressing persistent build-up challenges encountered in various processes. High moisture content and the stickiness of certain ores contribute to material accumulation on machinery, which can hinder workflow and reduce productivity. By utilizing the patented Slipcoat® technology, mining companies can significantly mitigate this issue, leading to increased operational efficiency.
Previously available only in South America, Slipcoat® has now strategically expanded its operations with new facilities in North America. This launch paves the way for a rapid expansion into the U.S. and Canadian markets, reflecting the growing demand for its innovative non-stick technology in the mining sector. The expansion underscores Slipcoat’s commitment to meeting the needs of a broader customer base and enhancing the efficiency and sustainability of mining operations across the continent.

The application of Slipcoat® is crucial in enhancing productivity. By preventing build-up in critical equipment such as haul trucks, chutes, and excavators, the coating allows for smoother operations and reduces the need for frequent cleanup. This translates to less downtime during working hours, thereby yielding a higher volume of processed materials.
Moreover, implementing Slipcoat® effectively reduces maintenance costs. Traditional maintenance practices often involve intense labor to clear built-up materials, which can lead to equipment wear and tear. With Slipcoat®, the need for such extensive maintenance is minimized, allowing operations to be more cost-effective and streamlined.
Additionally, eliminating build-up reduces safety concerns, as employees are less likely to be injured while manually removing materials from large machinery.

Slipcoat® has applications across various types of machinery used in mining operations. Essential equipment such as haul truck boxes, loader buckets, rail cars, and chutes can all greatly benefit from the coating’s properties. In addition to these, it can be applied to crushing stations and pan feeders, where material handling is critical.
The versatility of Slipcoat® makes it suitable for multiple operational environments. Whether in open-pit mines or underground settings, the product adapts well and maintains its efficacy under differing ore characteristics and temperatures. Its non-stick properties enhance the performance of the machinery it coats, allowing for smoother transitions and fewer interruptions in operations.
The key selling point of Slipcoat® is its unique ability to form a protective, non-stick barrier. This patented technology penetrates the metal surfaces of mining equipment, thereby creating a robust layer that effectively repels build-up. This feature not only ensures that machinery operates optimally but also extends the lifespan of the equipment by reducing abrasive contact with accumulated materials.

The application process for Slipcoat® is advantageous for mining operations. The non-permanent advanced filming technology can be sprayed on in seconds and allows for low usage with 1 gallon covering up to 800 square feet. This rapid application contributes to the overall efficiency of mining operations, enabling employees to focus on more critical tasks rather than spending excessive time on machinery maintenance.
Slipcoat is known for its robust performance at extreme temperatures, maintaining efficiency from -40°F (-40°C) to over 100°F (38°C). This makes it ideal for demanding mining conditions. The benefits are seemingly endless as it provides significant operational benefits: a 50% reduction in water use during equipment cleaning, a 25% to 30% increase in load volumes, and it is 99.8% biodegradable, holding the USDA Bio-Preferred certification.
One of the standout features of Slipcoat® is its environmentally friendly composition. As sustainable practices are increasingly prioritized in various industries, the demand for products like Slipcoat® is likely to grow. The use of biodegradable constituents ensures that the product does not harm surrounding environments, making it suitable for use in sensitive ecological areas often associated with mining activities.

In addition to environmental benefits, Slipcoat® is completely non-toxic, ensuring safety for workers who apply or operate machinery treated with the coating. This is particularly critical in confined spaces common in underground mining, where air quality and health safety are paramount concerns.
Slipcoat® also plays a key role in reducing employee injuries related to maintenance. Traditional practices, which often require workers to physically scrub or pry away built-up materials, carry a high risk of accidents. By preventing the accumulation of these materials, Slipcoat® effectively lowers the risk of injury and enhances overall workplace safety.
The future looks bright for the global adoption of Slipcoat®. As awareness of its benefits grows within the mining sector, there is significant potential for expansion into new markets. The technology can be utilized beyond just mining, potentially extending to other areas such as rail transport and processing facilities, thereby broadening its applicability.
Slipcoat® has established a solid presence in the mining industry, with an impressive roster of notable clients. Companies such as Vale, Cemex, Kinross, Boleo, LHG Mining, Bemisa, and Ternium exemplify the trust leading mining operations place in Slipcoat’s advanced coating technology. These partnerships highlight the product’s effectiveness in improving operational efficiency, reducing maintenance needs, and enhancing safety standards. The adoption of Slipcoat® by such significant industry players underscores its reputation as a reliable and impactful solution for addressing buildup and maintenance challenges in mining.
Kinross Gold Corporation has reported favorable outcomes from the implementation of Slipcoat® in their mining processes. Feedback suggests significant reductions in equipment maintenance time and a marked increase in operational efficiency, affirming the product’s role as a transformative addition to mining practices.
The versatility and efficiency of Slipcoat® present significant growth opportunities not only within the mining industry but also in adjacent sectors. As industries around the world seek to improve productivity, reduce costs, and maintain safety standards, the adoption of Slipcoat® may become increasingly sought after.
Slipcoat® represents a pivotal advancement in mining technology, poised to make a substantial impact on operations worldwide. By addressing the persistent challenges of build-up, enhancing productivity, and promoting safety, it is set to become an indispensable resource in the mining industry.
For more information:
1-888-734 SLIP
info@slipcoat.com
1050-12471 Horseshoe Way
Richmond, BC, Can, V7A4X6