Standard produces high-purity lithium carbonate

The 45,000-acre Bristol and Cadiz Dry Lake lithium brine project is located in the Mojave Desert, San Bernardino County, California.
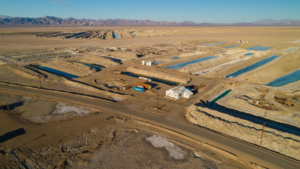
Standard Lithium Ltd. [SLL-TSX, STLHF-OTC-Nasdaq-Int. Designation, S5L-FRA] said Wednesday it has completed the commissioning process for its prototype crystallisation pilot plant and has produced its first quantity of high purity lithium carbonate.
The company, via its technology partners, is currently designing and fabricating both halves of its full-scale pilot plant. The Lithium Extraction Pilot Plant is being designed and built by Zeton Inc. in Burlington, Ontario. The Lithium Carbonate Crystallisation Pilot Plant is being designed and built by Saltworks Technologies Inc. at their facility in Richmond, B.C.
Both parts of the plant are based on Standard Lithium’s proprietary technology.
Standard Lithium shares were unchanged at 99 cents on Wednesday. They trade in a 52-week range of $2.61 and 80 cents.
Brines (in salt ponds) and spodumene (hard rock) represent the two main sources of commercial lithium production.
Standard Lithium is focused on unlocking the value of existing large-scale U.S.-based lithium brine resources that can be brought into production quickly.
It is working to achieve that goal at a time when lithium has emerged as a hot commodity due to its role as a principal ingredient in lithium-ion batteries used in electric vehicles and mobile phones.
“There are brine projects that have been overlooked because previous operators have elected to apply conventional mining processes to them,” said Standard Lithium CE0 Robert Mintak. Standard Lithium, by contrast, has developed a lithium extraction process that reduces the recovery time for extracting lithium from a number of years to as little as several hours.
The company’s flagship asset — the 180,000-acre “Smackover Project — is located in southern Arkansas, the most prolific and productive brine region in North America.
On Wednesday, the company said the newly-constructed crystallisation pilot prototype was operated using a relatively impure feed solution similar to, but less pure than that produced by the company’s lithium extraction process.
The feed solution contained approximately 4,500 mg/L lithium, 5,000 mg/L sodium (at least one order of magnitude higher than that produced by the company’s lithium extraction process), over 400 mg/L of other alkali, alkaline earth and transition metal contaminants, and over 900 mg/L of other non-metallic anionic contaminants.
After setting up and completing initial commissioning work for approximately two weeks, the prototype pilot circuit was operated, whilst monitoring crystallisation progress using high-speed, multi-image photo-microscopy and artificial intelligence computer image recognition for crystal size and shape.
After rudimentary washing of the resulting crystallised solids, analysis confirmed that the purity of the product exceeded >99.1% lithium carbonate.
The prototype pilot plant is now undergoing routine optimisation to adjust several key operating parameters. In addition, the number of crystallisation cycles that have been operated will be increased, and additional product washing technology will be introduced to enable further process optimisation and improved product purity.
The technical team will also be adjusting the composition of the input feed stream so as to optimize how the two parts of Standard Lithium’s proprietary technologies work together.
The company’s technical team is currently gathering data to allow it to start the design of a larger scale crystallisation pilot plant that will be deployed at Standard’s project site in Arkansas.