New Battery Energy storage System Lowers Costs and Increases Efficiency
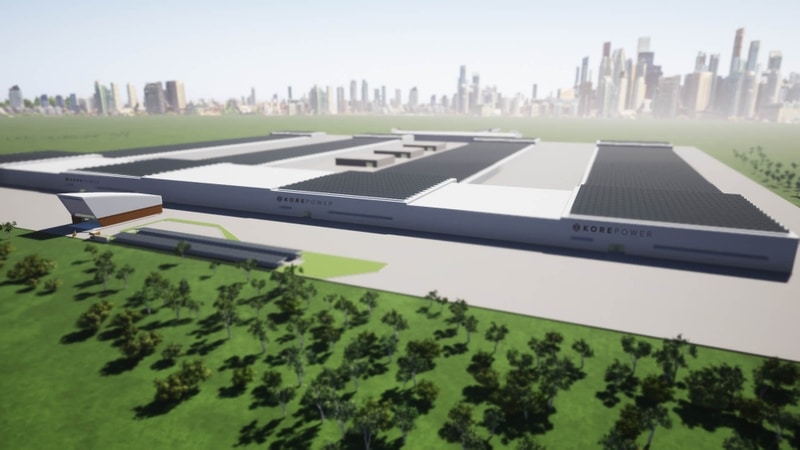
By Jane Foutz
Engineers at KOREÂ Power, based in Coeur d’Alene, Idaho, are developing high-density, high-voltage energy storage solutions for global, industrial, and mission-critical markets. They have designed the 1500 volt Mark 1™ Energy Storage System, which is scalable to any energy demand and is designed to operate in both off-grid and grid-tied environments. Developed to decrease installation and operation costs with higher efficiency, the Mark 1 includes proprietary lithium, nickel, manganese, cobalt, (NMC) cells and modules, with advanced safety features, managed and optimized by the Mark 1 battery management software (BMS).
KORE Power’s lithium-ion technology features the highest energy density available in the 1500V class optimized for containerized installations, which facilitates smaller, more efficient and safer energy systems for microgrids, electric vehicle charging stations, and 5G towers. In addition to these design elements, KORE Power’s proprietary manufacturing technique incorporates a patented stacking method to compensate for and protect against thermal expansion, which naturally occurs during charge and discharge cycles. This enables the cell to remain stable over thousands of cycles.
KORE Power is focusing its efforts on evaluating the Mark 1™ module and rack, with testing to conform to Underwriter Laboratory (UL) 1973, UL 1998, UL 991, UN 38.3, and IEC 62619 requirements. UL wrote the majority of the industry safety standards and is considered the benchmark that every testing lab adheres to. The KORE Power certifications are related to battery use in stationary energy storage, in the BMS, and in transporting methods for the lithium-ion batteries. The company has also begun shipping modules and racks that do not require 9540A, which addresses safety concerns identified by the building codes and the fire service in the United States, Europe, India and Australia. The first shipments are going to customers and partners, which will enable them to begin using the Mark 1™ cells, modules and racks for stationary energy storage applications. The company expects to ramp up Mark 1™ Energy Storage System production to participate in large installations in 2020.
“Successful completion of our second round of product certification testing represents a major growth milestone for KORE Power. We’ve promoted the safety, efficacy and density of KORE Power’s Mark 1™ battery cell, and now we’re able to prove these benefits and fulfill orders for the Mark 1™ for integration into large-scale energy storage systems across the globe,” said Lindsay Gorrill, CEO of KORE Power. “Further, we recognize the importance of 9540A testing, particularly with the industry’s push and efforts to enhance safety around battery technologies. We’re pleased to be a part of the industry’s shift to supply safer battery products.”
KORE Power recently announced that it has entered into a Memorandum of Understanding (MOU) with Northern Reliability, Inc. (NRI), a United States-based energy storage system integrator and control systems and software manufacturer. The MOU is a strategic alliance between KORE Power and NRI for energy storage projects, allowing the companies to combine their expertise and efforts to increase business and sales opportunities using NRI’s energy storage system engineering, procurement, and construction services, and KORE Power’s Mark 1™ Battery Energy Storage System.
NRI recently announced its commercial and utility-scale energy storage solutions ranging from 0.5 megawatt hours (MWh ) upwards to 400 MWh. These recent advances enable NRI to work with its utility customers to develop an operating model that takes advantage of potential revenue streams to assist in offsetting operating costs. This strategic alliance allows NRI to offer the Mark 1™ Battery Energy Storage System to its customers as part of its energy storage solution. KORE has the production capabilities to manufacture industry-leading lithium batteries in any size and configuration to suit unique design requirements.
“KORE Power brings to the table a critical element which NRI has been searching for in its stable of high-quality components: A domestically produced lithium energy storage system of the highest quality. Not only can the NRI-KORE alliance help to solve some of the supply-side security concerns of the US governmental entities and US utilities, it also offers a cost effective solution, which provides comparable performance to other foreign-made suppliers, with reduced freight costs and product lead times,” remarked Jay Bellows, President and CEO of NRI.
“Working with NRI is a commanding move towards increased integration of KORE Power’s battery products across North America. We are excited to work with the NRI team in a market where energy storage solutions are in high demand,” said Lindsay Gorrill, CEO of KORE power. “Together, our companies will promote and sell a joint solution that is ideal for the North American market as it shifts to accommodate cleaner, more sustainable energy practices across a variety of applications.”
KORE Power is working with integration partners to design microgrid and mining ready solutions. These solutions will benefit the mining community by helping to eliminate the transportation of diesel into remote sites, providing clean energy options to off-grid and remotely located mines and reducing downturn caused by outages.
KORE Power is also developing plans to build a lithium-ion battery manufacturing facility in North America. This facility will serve the growing demand for end-of-life battery management in applications such as fossil fuel peaker plants (gas turbines or gas engines that burn natural gas), wind and solar plus storage projects, energy storage units powered by behind-the-meter systems, such as wind turbine, solar photovoltaic, or combined heat power units, and Micro-grid optimization. Another area of end-of-life battery management demand is E-Mobility, which is the concept of enabling vehicle and fleet electric propulsion. These e-Mobility efforts are motivated by the need to address corporate fuel efficiency and emission requirements, as well as market demands for lower operational costs. Other end-of-life battery management demands come from mining energy solutions, and the military.