Looking at the future of electric vehicles
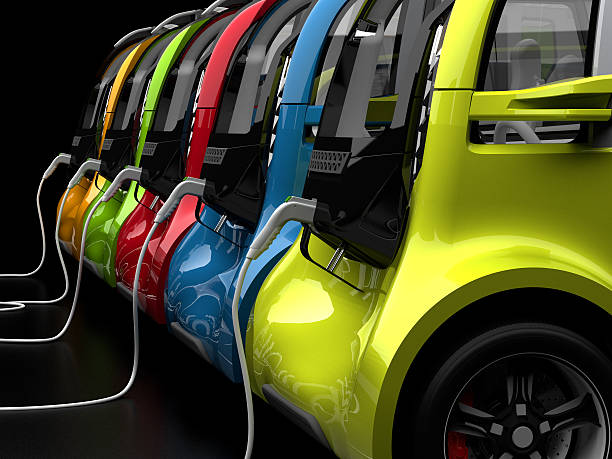
The rapidly growing electric vehicle industry will have a significant impact on the mining sectors targeting battery minerals
By Jane Foutz
Benchmark Mineral Intelligence, headquartered in London, England, is a price reporting agency that provides market intelligence for the lithium-ion battery (LIB), electric vehicle (EV) and energy storage supply chains.
Benchmark recently hosted the EV Seminar Series 2020 (EV Fest). In keeping with the times, Benchmark live-streamed the free virtual conference, hosting sessions on developments in electric vehicle (EV) charging, infrastructure, and associated battery technologies. They also discussed the outlook from countries such as China, Japan, Korea, EU, UK, and the USA and how companies are adjusting to the post-COVD landscape. Following are some highlights from those sessions.
The Covid-19 fallout from most companies was reported as minimal. Facility construction continues and the pipeline is strong. Consensus was that the down-stream slowdown will work its way upstream in the second half of 2020, but production will not be severely impacted. China’s production has reportedly recovered. Presenters expect the worldwide market to come back and increase growth beyond 2021.
According Simon Moores, Benchmark Managing Director, we are in the midst of a “battery arms race” with China dominating in EV battery processing capability and supply chain. The cumulative building of global LIB mega factories (>1gigawatt-hours) has gone from three plants in 2015 to 136 plants in 2020. In the last 12 months, China has built 46 plants, the equivalent of one per week, Europe is next with five, and the USA is behind that with three new plants, or the equivalent of pne new plant every four months.
Andrew Miller, Benchmark Product Director, noted that China owns most raw materials for anodes and the largest share of cathode production. The USA is ramping up LIB production, but by 2029, Miller says China will still be ahead with about 71% of the LIB production.
In discussing future battery technologies, Cairn Energy Research Managing Director, Sam Jaffe, from Boulder, Colorado, said that LIBs are now 30 years old and have been greatly improved. He said that many new battery technologies are “skating to the puck,” meaning when new technologies are developed, they can’t match the improvements in lithium-ion technology, which becomes cheaper, and lasts longer with each change. Jaffe predicts that the successful new technologies will be the ones that improve the LIBs. By 2030, he predicts silicon-rich anodes and manganese-rich cathodes will be the new technologies that improve the LIBs.
Kurt Kelty, VP of Automotive Sila Nanotechnologies, located in Alameda, California, said his company is providing battery materials that require no significant supply chain manufacturing alterations. Sila provides battery materials that drop into existing infrastructures. This means that battery manufacturing partners can produce higher performing cells in their factories on existing production equipment. This also means that automakers and consumer product companies can continue working with their battery suppliers while seamlessly incorporating Sila’s materials technology into new products. Without equipment changes to cause delays, companies will not increase their capital expenditures or their overhead.
According to Kelty, to mass market electric vehicles, manufacturers must lower the cost of the battery pack on a dollars per kilowatt-hour (kWh) basis. The best way to do this is through higher volumetric energy density, which Sila materials enable. More energy in each cell means fewer cells for the same battery pack capacity, increased vehicle range, and much lower costs overall. And, Kelty says, this results in reduced depreciation per watt-hour (Wh), reduced carbon dioxide emissions per Wh, and reduced warehouse space for anode per Wh.
Sila’s first product is an anode material, which Kelty says increases battery density by 20-40% and is in qualification trials with multiple OEMs. Sila manufactures and ships the battery materials to cell makers for batteries used in consumer devices, such as mobile phones, electric vehicles, electrified flight, and grid storage. For cell material suppliers, Kelty says this battery density increase will result in faster growth for materials that store energy, for example, cathodes. He predicts slower growth for components that don’t store energy, such as casings and top caps. But, he says there will be lots of growth to go around.
Looking at the essential issue of changing stations, Rho Motion Managing Director, Adam Panayi, said EV manufactures are assessing what adequate charging coverage looks like, what technologies will dominate battery technologies in the future, and what all this will cost.
A working example of charging coverage was presented by Andrew Daga, CEO of Momentum Dynamics. Headquartered in Malvern, Pennsylvania, Momentum produces high-power wireless charging for electric vehicles. Malvern said the transportation and energy industries are undergoing massive change as EV adoption accelerates across the world and as the critical fueling infrastructure scales with it. Wireless charging offers reduced cost and increased efficiency in refueling autonomous and electric vehicles. Cities are moving toward electric vehicles for public transportation, but limited battery capacity (range) has hindered their growth. Momentum Dynamics’ wireless, high-power charging systems can provide unlimited range to fleets with set routes.
Momentum’s charging system facilitates on-route charging. Electric buses can now outperform diesel-fueled and hybrid buses in terms of extending the vehicle’s driving range-while eliminating harmful tailpipe emissions to zero and significantly reducing overall costs of operation. The system is installed in the road, which allows buses parked above it to be recharged multiple times per day during their scheduled stops.
While at a stop, charging occurs at 50 to 450 kilowatts of power while a bus is loading or un-loading passengers. Taxis and delivery vans would not have to return to their depots for charging, saving the cost of backup vehicles, as well as the cost of trips back and forth to the depot to recharge.
Tackling the problem of EV battery disposal and reuse, Mohamad OMar from the California Department of Toxic Substance Control, said battery recycling is critical in the long term, and the low value of recovered materials represents a challenge to raising the capital needed to ramp up the recycling infrastructure.
However, Vancouver-based American Manganese Inc. [AMY-TSXV] has developed the technology to recycle spent lithium-ion batteries.
LIBs have a useful EV life of 10-20 years. Large-scale retirements of these batteries will occur in the next 5-10 years, and their disposal represents a major environmental concern. LIBs are potentially valuable during their second life, for example energy storage that uses recycled materials. To address the EV battery disposal challenge, California has created the California Lithium-ion Battery Recycling Advisory Board.